The CAD program uses very different graphics, so I will have to find a format in common. I'll see what I can do.
screen capture as a jpeg?
Thanks for the suggestion, JFB. Sometimes I over-think things.
Here is the constraints layer:
For perspective, imagine you are standing outside the car, off of the right (passenger) rear tire, looking toward the steering wheel.
The fire wall is obvious, the roughly rectangular pattern top center is the roof line from an interior point of view, the angled segments top and right are the A pillars along either side of the windshield, and the green balls are the left and right ends of the dash board where the cage has to clear them.
Next I've turned off the constraints and turned on the tubing layers:
Here the main hoop, the horizontal brace that goes across the cockpit at the shoulder belt attach line, and the side hoops that surround the door openings, are the only parts that have been mocked up so far. The rest only exist in the drawing, and are subject to change. I'm sure I will have to adjust the X brace at the fire wall to allow for access to the engine hatch. The struts back to the rear wheel house attach points are just a first guess also.
Here is the constraints layer:

For perspective, imagine you are standing outside the car, off of the right (passenger) rear tire, looking toward the steering wheel.
The fire wall is obvious, the roughly rectangular pattern top center is the roof line from an interior point of view, the angled segments top and right are the A pillars along either side of the windshield, and the green balls are the left and right ends of the dash board where the cage has to clear them.
Next I've turned off the constraints and turned on the tubing layers:

Here the main hoop, the horizontal brace that goes across the cockpit at the shoulder belt attach line, and the side hoops that surround the door openings, are the only parts that have been mocked up so far. The rest only exist in the drawing, and are subject to change. I'm sure I will have to adjust the X brace at the fire wall to allow for access to the engine hatch. The struts back to the rear wheel house attach points are just a first guess also.
With the stiffener installed, I can finish the mid-rocker and front wheel well surround repairs. The larger, trapezoid shaped piece was a bear; took a couple of tries to get it right.
I decided to put a drain / access hole here, so I can spray primer and rust proofing inside later:
Finishing up here:
Now I need to rebuild the bottom of the A pillar itself. I chose to use a simple wedge shaped structure. This will restore the original strength, but was also a minor goof up, as I’ll describe in a bit:
I find that the contour filler panel and fender are rust damaged up a little higher than I thought, so another 1/2 inch or so has to come off:
Here I test fit a piece of metal to repair the outer rocker; making sure it will mate up with the work I’ve done so far:
Now to weld in the A pillar repair:
Here is just a small leveling piece. At the factory they just pinched the rocker flange in here and spot welded the snot out of it. This area was very uneven, so it will help to have a clean flat piece to weld on:
Here is what I meant by a minor goof up. That steel rod you see at right center is laid in the door sill; it helps me line up things. In the previous pic, you can see that it misses the A pillar repair piece by a 1/4 inch or so. That part of the outer rocker that forms the door sill, continues forward to form the flange where the rocker and fender panel join. It should also be tack welded to the A pillar for support. Oops. Likewise, the bottom of the contour fill panel extends down to the same flange, and lays flat against the A pillar. Oops. I need to add a piece to bring the A pillar out further here. It is mostly cosmetic, so a light piece should do:
Next I’ll add a backer strip behind where the original metal and new metal join. This helps two ways. In many places, it is not necessary to weld a full bead along a junction like this; a good spot weld every 1/2 inch or so is enough. I also do not have to trim the edges so perfectly. When I’m done with the metal work, I’ll back fill this junction with epoxy, and she’ll be good as new.
Now I use the steel rod again to position the piece of the door sill I cut out earlier, and weld it back in:
Can you guess what this is going to be?
Now?
Now??
Here is where it goes:
Next to replace the bottom of the fender panel I had to cut off:
Fitting the new pieces along with the old:
Adding a backer strip:
More fitting
The repair of the fender ready to install:
When crimping an edge, I use the extra piece of metal as kind of a pad, so as not to leave jaw marks on the finished piece:
Finally ready to weld it up:
I added a backer strip to this original piece:
And welded it in:
From the back side:
I should have used backers on this piece too, but didn’t. No choice but to weld it all around. The welding is not that hard; the post weld grinding is time consuming:
Finally, inside and out:
Next up: splash shields. Stay tuned.



I decided to put a drain / access hole here, so I can spray primer and rust proofing inside later:

Finishing up here:







Now I need to rebuild the bottom of the A pillar itself. I chose to use a simple wedge shaped structure. This will restore the original strength, but was also a minor goof up, as I’ll describe in a bit:





I find that the contour filler panel and fender are rust damaged up a little higher than I thought, so another 1/2 inch or so has to come off:



Here I test fit a piece of metal to repair the outer rocker; making sure it will mate up with the work I’ve done so far:

Now to weld in the A pillar repair:



Here is just a small leveling piece. At the factory they just pinched the rocker flange in here and spot welded the snot out of it. This area was very uneven, so it will help to have a clean flat piece to weld on:

Here is what I meant by a minor goof up. That steel rod you see at right center is laid in the door sill; it helps me line up things. In the previous pic, you can see that it misses the A pillar repair piece by a 1/4 inch or so. That part of the outer rocker that forms the door sill, continues forward to form the flange where the rocker and fender panel join. It should also be tack welded to the A pillar for support. Oops. Likewise, the bottom of the contour fill panel extends down to the same flange, and lays flat against the A pillar. Oops. I need to add a piece to bring the A pillar out further here. It is mostly cosmetic, so a light piece should do:


Next I’ll add a backer strip behind where the original metal and new metal join. This helps two ways. In many places, it is not necessary to weld a full bead along a junction like this; a good spot weld every 1/2 inch or so is enough. I also do not have to trim the edges so perfectly. When I’m done with the metal work, I’ll back fill this junction with epoxy, and she’ll be good as new.


Now I use the steel rod again to position the piece of the door sill I cut out earlier, and weld it back in:



Can you guess what this is going to be?

Now?

Now??

Here is where it goes:



Next to replace the bottom of the fender panel I had to cut off:


Fitting the new pieces along with the old:

Adding a backer strip:

More fitting

The repair of the fender ready to install:


When crimping an edge, I use the extra piece of metal as kind of a pad, so as not to leave jaw marks on the finished piece:

Finally ready to weld it up:



I added a backer strip to this original piece:

And welded it in:

From the back side:

I should have used backers on this piece too, but didn’t. No choice but to weld it all around. The welding is not that hard; the post weld grinding is time consuming:


Finally, inside and out:

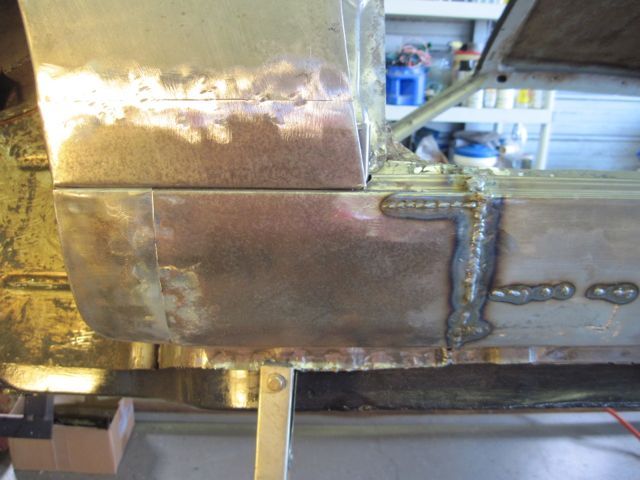
Next up: splash shields. Stay tuned.
Well done UFO. I love how you're tackling the tasks... lining em up and knocking em down. Hell...at this rate...you'll be driving it this summer...
UFO, You and I are performing a similar restoration. Albeit, yours a bit deeper. What gauge steel are you using?
There are several different gauges needed. Most all of the cosmetic panels are 22 gauge, so are the floor pans. The mid-rockers, front wheel well surrounds, and other structural bits are mostly 16 gauge. I've used some 18 gauge pieces also. I try to pay attention; been more than once I've made a piece of the wrong thickness and had to do it over. I can get small pieces of 22 and 16 locally, the others I have to order.
John, what are you working on now? Your gorgeous 5079 is all done, is it not? Rodney
John, what are you working on now? Your gorgeous 5079 is all done, is it not? Rodney
As you might imagine, after having to repair so much rust damage, I have a keen interest in preventing it from happening again. While I had it torn apart, I spent some time looking at it to see why the rust formed where it did, and what I could do to prevent it. Any place within sight of a tire needs extra attention for rust prevention. The tires throw up sand, rocks, road debris, water, salt, tar, and all manner of trash. This junk hits anything nearby like a corrosive sandblaster. Any coating will eventually be eroded away, exposing the metal, which will also succumb.
Rust also forms anywhere debris and water are trapped. It’s impossible to prevent all water and debris from getting inside the unibody structure, so it is important to give it a way to get out.
My approach is to coat the underbody metal with epoxy primer. In areas exposed to the tire blast, undercoating will be used as well. Splash shields will protect the most vulnerable areas, and be removable for repair or replacement as needed. Some extra drain holes may also be added.
I started making the templates for these shields before I finished the A pillar work, because the area is easier to get to. Here is the cardboard and tape mock up:
The lower round hole is for the antenna wire, which I’ll not be using, so I will plug it. I’ll make a cover for the obround hole in the longeron, and cover the upper round hole along with the gap that is exposed into the ventilation cowl.
Here the area is cleaned up and the obround hole is covered:
The shields are held in with sheet metal screws:
These pieces are ready for their first coat of paint. The center and right ones are for the left front wheel well / A pillar. The left one in this pic is for behind the left B pillar. It would normally be hidden by the gas tank.
The more complex shields are made in pieces. It is easier to make them that way, and also to install and remove them.
Stay tuned for my next installment! Rodney
Rust also forms anywhere debris and water are trapped. It’s impossible to prevent all water and debris from getting inside the unibody structure, so it is important to give it a way to get out.
My approach is to coat the underbody metal with epoxy primer. In areas exposed to the tire blast, undercoating will be used as well. Splash shields will protect the most vulnerable areas, and be removable for repair or replacement as needed. Some extra drain holes may also be added.
I started making the templates for these shields before I finished the A pillar work, because the area is easier to get to. Here is the cardboard and tape mock up:

The lower round hole is for the antenna wire, which I’ll not be using, so I will plug it. I’ll make a cover for the obround hole in the longeron, and cover the upper round hole along with the gap that is exposed into the ventilation cowl.
Here the area is cleaned up and the obround hole is covered:

The shields are held in with sheet metal screws:

These pieces are ready for their first coat of paint. The center and right ones are for the left front wheel well / A pillar. The left one in this pic is for behind the left B pillar. It would normally be hidden by the gas tank.

The more complex shields are made in pieces. It is easier to make them that way, and also to install and remove them.

Stay tuned for my next installment! Rodney
Hi Rodney,
Looks great. Just a thought...might you consider making them just a bit undersized and use some "bulb" type weather strip seal on them? This will offer a better seal than trying to cut it as exact fit.
Just food for thought....
Looks great. Just a thought...might you consider making them just a bit undersized and use some "bulb" type weather strip seal on them? This will offer a better seal than trying to cut it as exact fit.

Just food for thought....
Good idea, Rob. That looks like a JCW item, right? I think I will caulk / undercoat the semi-permanent shields in. Use the whether strip on those that need to come out more often, like in front of the right rear tire. I moved my battery tray there.
Rodney, my current project is 7159. The car is remarkably rust free above the rocker panels. However both rockers and the front valence are compromised. I not sure how this happened. Perhaps a flood car? regardless, I purchased the car knowledgably and have finished rebuilding the valence area and support frame behind it. I am now rebuilding the passenger rocker area. As you know, the work is slow as fabricating parts and reassembling the structure is tedious. I'll post some pics later of the effort. Since I removed the entire outer rocker, there is a bit more to see. I purchased Wilkinsons, not the factory's, outer replacement rockers. They are side generic requiring you to trim of the extra to fit the side you desire. I also bought replacement middle rockers. However, the passenger side will not require replacement. My fingers are crossed that when I remove the driver's side, it is also repairable. It will be nice to get my money back on those inner rockers. Wishing that I had a 40" metal shear.
I buy that kind of stuff from McMaster Carr Link
OK, now on to rust repairs to the bottom of the left B-pillar. First I strip away old paint, bondo, and some lead, so I can see the extent of the damage. At least that which can be seen from outside:
I’ll use some masking tape to section off the damaged parts, with attention to locate the spot welds and drains:
I may be able to save some of this outer rocker panel piece, but not what I find under it:
Now I have scuffed off the worst of the rust scale. I find what seems to be a good place to cut away the bottom of the B pillar:
This WAS 16 gauge steel:
So was this - the mid rocker:
Notice here the mid rocker is made in sections. I did not know this, and just happened to uncover a place where the lap weld is. Good to see the rust is only behind the B pillar.
This is the floor pan, just under and forward of where I am working. I spotted this damage earlier, and painted around it, knowing I would have to cut it out:
Cutting this away reveals the flange of the inner rocker rusted away too. I had to cut this out a little bit beyond what can be seen in this picture, to get back to solid metal.
I made a repair piece and welded it in, but did not get a picture of it.
Next to weld in a piece of 22 gauge to fill in the floor pan here.
Now I have all the rust cut out, and some of the pieces replaced. I mask the edges where I know I have more welding to do. Then I spray zinc primer inside, as I will not be able to it after this next patch:
This patch of 16 gauge steel was not too hard to make:
Next episode; I’ll make the B pillar structural repair, and start on some of the more cosmetic bits. Stay tuned.



I’ll use some masking tape to section off the damaged parts, with attention to locate the spot welds and drains:




I may be able to save some of this outer rocker panel piece, but not what I find under it:



Now I have scuffed off the worst of the rust scale. I find what seems to be a good place to cut away the bottom of the B pillar:


This WAS 16 gauge steel:

So was this - the mid rocker:


Notice here the mid rocker is made in sections. I did not know this, and just happened to uncover a place where the lap weld is. Good to see the rust is only behind the B pillar.
This is the floor pan, just under and forward of where I am working. I spotted this damage earlier, and painted around it, knowing I would have to cut it out:

Cutting this away reveals the flange of the inner rocker rusted away too. I had to cut this out a little bit beyond what can be seen in this picture, to get back to solid metal.
I made a repair piece and welded it in, but did not get a picture of it.
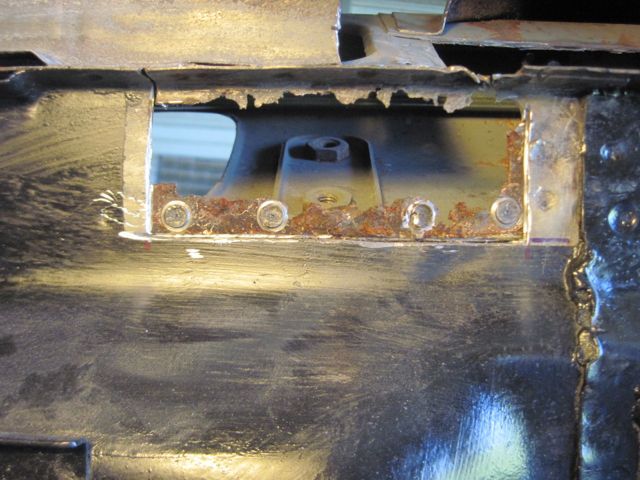
Next to weld in a piece of 22 gauge to fill in the floor pan here.

Now I have all the rust cut out, and some of the pieces replaced. I mask the edges where I know I have more welding to do. Then I spray zinc primer inside, as I will not be able to it after this next patch:

This patch of 16 gauge steel was not too hard to make:

Next episode; I’ll make the B pillar structural repair, and start on some of the more cosmetic bits. Stay tuned.
Thank you for posting how you are doing your restoration work, especially the photos. It is very instructive and helpful! I wish I had your talent and patience.
Jack
Jack
Rodney -
You must cry everytime you cut a piece away, and find 2-3 more places to fix... Or maybe you are expecting it....
Keep up the great work!
Rocky
You must cry everytime you cut a piece away, and find 2-3 more places to fix... Or maybe you are expecting it....
Keep up the great work!
Rocky
Pretty much expecting it by now Rocky. Some of the damage is obvious, and some leaves tell tale clues for me to find. What is cry - worthy is how much time it takes.
Jack, the patience I guess I was born with. The "talent" is just a matter of starting with the easier jobs and working up to the harder ones.
Oh, and lest I forget, a big part of "talent" is reading most everything that appears on this forum, and studying the work of Rob, Rick, Rocky, David, George, Comp2, Goran, Jack, JT, Johnny, Marlin, Larry; too many to name them all. A whole bunch of skill, talent, experience, and imagination is at your fingertips here.
Jack, the patience I guess I was born with. The "talent" is just a matter of starting with the easier jobs and working up to the harder ones.
Oh, and lest I forget, a big part of "talent" is reading most everything that appears on this forum, and studying the work of Rob, Rick, Rocky, David, George, Comp2, Goran, Jack, JT, Johnny, Marlin, Larry; too many to name them all. A whole bunch of skill, talent, experience, and imagination is at your fingertips here.
On the structural parts that are not cosmetic (will not be seen when finished), I do not worry too much about making it look pretty or original. I have also learned that trying to make multiple bends in a repair piece is a good way to end up with scrap metal. Now I keep the pieces as simple as possible, and make more complex pieces by welding simple pieces together.
Here is a template for this repair using just masking tape:
Next I remove the template and use it to rough cut the repair pieces. Meanwhile, I mask off the welding zones, and spray in more primer:
This repair is done in 3 pieces; a flat panel with two wedge shaped bits on either side:
A little welding tip: that ugly bit of scrap metal clamped nearby is what I call my arc strike target. It serves two functions. The first arc strike or two with a MIG are usually not good. The wire is cold and the gas is not flowing. I use a scrap of the same gauge of metal I am about to weld. A few test strikes there gets the wire hot, the gas flowing, and makes sure my set up is right before I move on to the real work.
Again I mask and spray primer after the repair pieces are welded in place:
A few inches rearward, there were some rust through spots here, where the rear quarter meets the outer rocker. I cut out the rusty part, made a patch piece, drilled through a couple of new drain holes (not visible in this pic), and welded in the patch:
And after some clean up work:
This is a good example of how hard it is to get the contours and bends exactly right. Just off by a tiny bit, and it is plainly visible. Later, after the first coat of epoxy primer, I’ll smear a bead of epoxy (like JB Weld) into this crease, and after it sets up, I’ll burnish it smooth to match the original contours.
Tune in again for my next episode; I’ll wrap up the repairs to this area.
Here is a template for this repair using just masking tape:

Next I remove the template and use it to rough cut the repair pieces. Meanwhile, I mask off the welding zones, and spray in more primer:


This repair is done in 3 pieces; a flat panel with two wedge shaped bits on either side:



A little welding tip: that ugly bit of scrap metal clamped nearby is what I call my arc strike target. It serves two functions. The first arc strike or two with a MIG are usually not good. The wire is cold and the gas is not flowing. I use a scrap of the same gauge of metal I am about to weld. A few test strikes there gets the wire hot, the gas flowing, and makes sure my set up is right before I move on to the real work.
Again I mask and spray primer after the repair pieces are welded in place:

A few inches rearward, there were some rust through spots here, where the rear quarter meets the outer rocker. I cut out the rusty part, made a patch piece, drilled through a couple of new drain holes (not visible in this pic), and welded in the patch:

And after some clean up work:

This is a good example of how hard it is to get the contours and bends exactly right. Just off by a tiny bit, and it is plainly visible. Later, after the first coat of epoxy primer, I’ll smear a bead of epoxy (like JB Weld) into this crease, and after it sets up, I’ll burnish it smooth to match the original contours.
Tune in again for my next episode; I’ll wrap up the repairs to this area.
This area was badly rusted out, and after taking it apart, it is easy to see why. I’ve cut away the top part of the outer rocker here (what was left of it). It used to extend all the way back to the B pillar, where just a notch was cut out of it, and it continued rearward. The door striker cosmetic panel was curved down and forward, lapped over, and welded to the rocker / door sill about where my cut line is in these photos. This formed a wedge shaped little cavity just perfect for trapping all sorts of dirt, trash and water in there.
The masking tape helps me rough out the shape of the patch needed:
Here is the rough cut:
After some trimming and contouring:
I decided to use backer strips on this one, so I do not have to get it so perfect:
Test fitting looks good so far:
Clamping it in place to be sure it fits up right:
Next I have to make up pieces to patch the quarter panel and the top flange of the outer rocker:
The bottom of the outer rocker piece had some rust through holes too, so I made a patch for it:
Here I am just test fitting the repaired piece:
And the other repair pieces are taking shape:
More test fitting:
I flanged the top of this piece:
This little piece is needed to fill in a gap:
One last test fit with all the pieces in place:
Now to start welding:
One of the challenging questions is which piece to do last. It is easy to paint yourself into a corner, so to speak:
I do not have a pic of the repair after clean up. I’ll try to remember to take one. It looks better than this.
Tune in again for my next episode; the infamous rear wheel house repairs!

The masking tape helps me rough out the shape of the patch needed:


Here is the rough cut:

After some trimming and contouring:

I decided to use backer strips on this one, so I do not have to get it so perfect:

Test fitting looks good so far:

Clamping it in place to be sure it fits up right:

Next I have to make up pieces to patch the quarter panel and the top flange of the outer rocker:

The bottom of the outer rocker piece had some rust through holes too, so I made a patch for it:

Here I am just test fitting the repaired piece:

And the other repair pieces are taking shape:


More test fitting:

I flanged the top of this piece:

This little piece is needed to fill in a gap:

One last test fit with all the pieces in place:

Now to start welding:



One of the challenging questions is which piece to do last. It is easy to paint yourself into a corner, so to speak:

I do not have a pic of the repair after clean up. I’ll try to remember to take one. It looks better than this.
Tune in again for my next episode; the infamous rear wheel house repairs!
If your doing that kind of work to the doors, it wouldn't hurt to put the door on and check fit. I cut the door jam on mine and pulled it out fitting new metal to make the doors fit better:
I also welded music wire to the fender to tighten the gap making a real nice fit:



I also welded music wire to the fender to tighten the gap making a real nice fit:


Yes, I will be doing that; thanks for posting your work on this. I remember reading it at the time.
I'm waiting on a new set of striker - receivers, so I will get back to this task when they arrive. I also had to buy new doors; mine were rusted beyond saving, so I will have quite a lot of "fitting" to do.
Question for you - did yours fit this badly? I remember this area was heavily leaded up when I took it apart.
I'm waiting on a new set of striker - receivers, so I will get back to this task when they arrive. I also had to buy new doors; mine were rusted beyond saving, so I will have quite a lot of "fitting" to do.
Question for you - did yours fit this badly? I remember this area was heavily leaded up when I took it apart.


Add Reply
Sign In To Reply